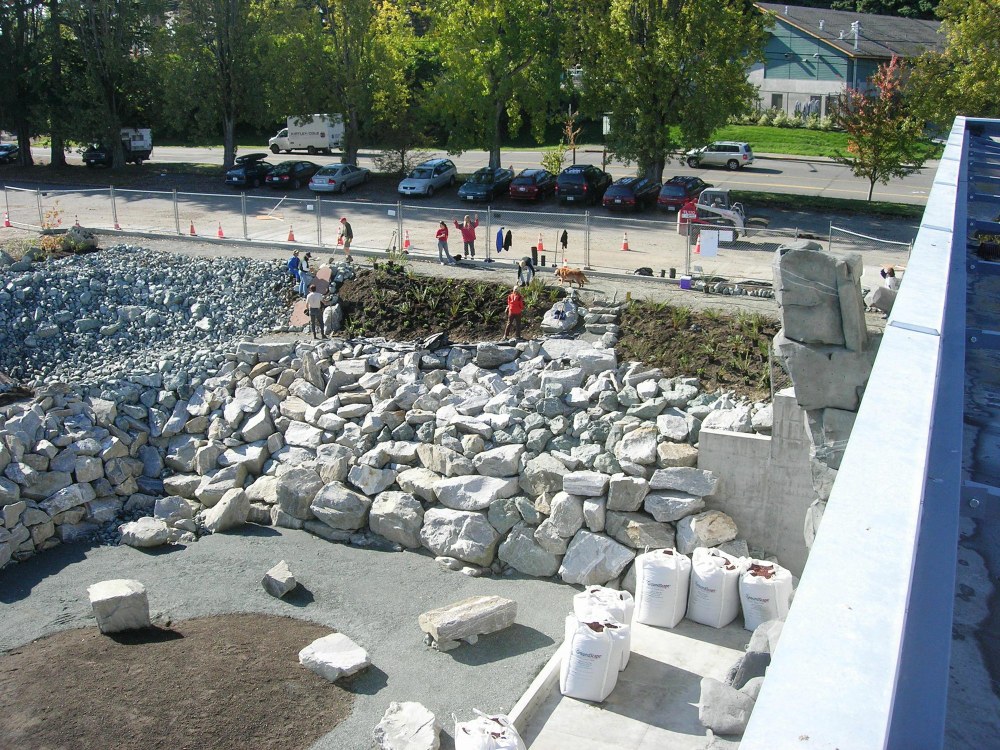
In 2007 a terrific team of volunteers worked together to renovate and build the impressive community facility we have today. Check out photos from the renovation and learn more about what it really took to turn Navy Building 67 into The Mountaineers Seattle Program Center.
Hazard abatement & general clean up
The first task under the general contract was abatement of hazardous materials. This included asbestos (steam pipe insulation, window glazing, floor tile and tile adhesives), lead (paint and battery work bench top), mercury and PBCs. The hottest lead paint was in the administrative/bookstore/small multipurpose rooms ceiling. An undisclosed 100 gallon waste oil tank was discovered under the lobby and 2 petroleum spills in south slope (~10 yards of material were removed). Fortunately the City of Seattle was responsible for both of these clean ups and the city worked with the Navy on these abatement costs.
In addition to abatement, remediation to achieve current Seattle Building Codes included seismic stiffing (~$82,000 of structural steel), insulation (on top of roof, on ceiling in lower level, walls included both a sprayed foam and fiber glass to achieve code, ~$62,000), fire sprinkler system (included lower level, behind the south climbing wall and under the canopy, ~$71,000), stabilization of ECA (environmental critical slope) around the South Plaza. Demolition costs were ~$142,000 including abatement.
Volunteer efforts recorded (many efforts were not recorded)
- 213 people volunteered at 106 Magnuson Work Parties investing a total of 4864.75 hours.
- 76 people volunteered at more than 2 Magnuson work parties, 23 more than 10, 9 more that 20 and 5 more than 30.
- 47 people volunteered more than 20 hours at Magnuson work parties, 28 more than 40 hours, 11 more than 80 hours, 7 more than 120 hours, 6 more than 160 and 3 more that 200 hours.
Fun food fact: To fuel our volunteers we spent $921 at Starbucks and $2834 at Zeeks Pizza.
Reduce, Reuse, Recycle!
Volunteers deconstructed both the floor of the building and the 80x90 ft shed on the south side of the building by hand. Some of this material was salvaged and used in north storage and to build some rafters. In fact, wood and labor from both deconstruction projects resulted in over $10,000 credit from our general contractor Saltaire. Without these salvage efforts the material would have ended up in a landfill.
Money saved from salvage helped pay for the newer building canopy design. All the nails from salvaged materials were removed by Mountaineers volunteers from all beams, posts, and rafters. They were all checked twice, once by eye and once with a metal detector. No nails were hit by the mill when some were re-sawed and others were planed.
The window infills on the eastside and one on the northwest corner of the building were painted by volunteers during Magnuson Work Parties. We received ~$1,000 credit for this task and several Mountaineers had a lot of fun driving the articulating lift for painting. The contract also allowed the Mountaineers to use their construction equipment during off hours and weekends for our volunteer work.
A number of Mountaineers became proficient at operating the big fork lift, parks small forklift, front end loaders, successor lifts, articulating arm lifts, back hoe, a small track hoe, and Bob Cat. At one work party we had 5 of these operating at the same time!
The brick walls on the north and south ends are unreinforced masonry. The Navy built them that way so they could be easily demoed for expansion. To meet the current seismic code we added steel structure inside the building. The 6” steel washers, visible on the outside, are bolted to this structure. Also all roofs have a ½” plywood sheathing nailed to the car deck roof for seismic stiffing. All roofs are also bolted to the poured concrete walls or steel structure.
Meeting Mountaineers instructional requirements
The Magnuson Instructional Requirements Group spent 2 years prior to construction defining all the features required to teach as much as possible at Magnuson. Instructional amenities at Building 67 was to have all the features of Camp Long, Sherman Rock, Spire Rock, some of Mt. Erie, and some features we haven’t had a good place to instruct and practice like following and cleaning a climb leader.
Fun anchor Facts:
- We build 34 floor anchors in Goodman Hall. That might not sound like a lot, but they're strategically placed – for climbers and social events.
- Using those floor anchors, we can rig 8 prussik ropes at one time. That’s a lot of self rescue!
- Other floor anchors allow climbers (at the same time that the prussiking is going on) to set up 3:1 (“Z”) pulley systems. We often teach both prussiking and the 3:1 at the same time as part of the glacier travel/crevasse rescue/(and maybe someday canyoneering).
- For social events, we had to figure out a way to install the anchors close enough to the wall so someone leaning against the wall and chatting wouldn’t get a shoe caught in the hanger or ring. That took a little doing.
- We've planned ahead: the floor in in Goodman C has 10 adapter holes where hangers can be installed if needed. Those took some careful concrete drilling.
- Not counting the South Plaza, the North Roof, or the basement, we have about another 35 hangers at various locations inside the building.
The climbing anchors on the north and south ends of the building are 2”x6” tube steel that’s 3/8” thick and bolted to the seismic stiffing. We built them beefy enough to handle climbing loads.
The final requirements document for these anchors and more was 48 pages long. Requirements covered most of our courses and branches: Basic Climbing, Intermediate Climbing, Crag, Water Ice, Aid & Big Wall, Small Party, Self-Rescue, Alpine Scramble, Backcountry Skiing and Snowboarding. The final document was converted to a Power Point format and iterated 9 times with candidate vendors to best ideas and cost function tradeoffs.
Most all steel and metal was sorted out to recycle. Also most wood was sorted out and cleaned up so that it could be recycled. We were unable to achieve our LEEDS goal because of the cost. We did everything on the list that we could afford.
Landscaping
All the soil preparation and planting were done by volunteers at Mountaineer Magnuson Work Parties, except for planting most of the trees and blowing in mulch. We received $11,635 credit for this effort. The Olympic Nursery planted 7 maples, 11 dogwoods, 3 pines, and a hemlock they donated. The Mountaineers also had a big impact:
- 80 volunteers planted 636 shrubs at the Presidents work party
- 35 volunteers planted 1193 ground covers at one work party
- An unrecorded number of volunteers transplanted 4 hemlocks from the terrace of the old building
Boulder Field
We hauled over 380 tons of boulders from East Valley Sand and Gravel for the boulder field in south plaza. Over 30 truck loads of boulders plus quarry spall, river run, and the smaller size gravel. Every boulder was selected by a Mountaineer and each placement involved a negotiation between the Geotechnical special inspector and a Mountaineer (Ohlson, Anderson, Eades or Yore). There is an 8” drain tile behind the first row of boulders that leads just outside/south of the fall zone curb and drains into a storm sewer near the east side of the south plaza.
THank you!
It goes without saying that none of this would have been possible without the incredible work of our dedicated volunteers. We've grown into this space over the years, and most recently completed our Friction Slabs project. Thank you to everyone who pitched in, got dirty, and helped us make this the best recreational education center in the world (that's our opinion anyway).